Diagnosing and Preventing Burn Marks in Plastic Injection Molding
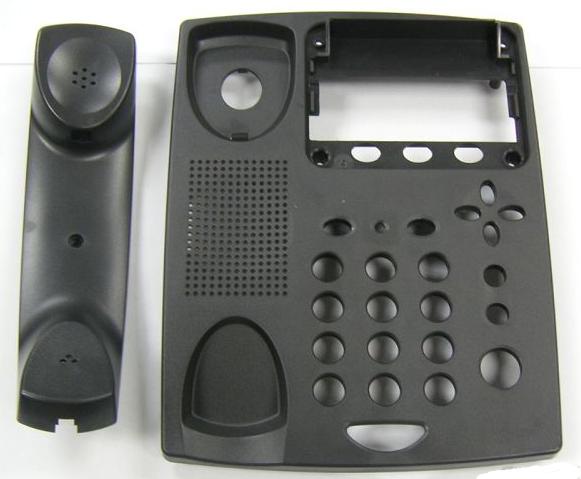
Diagnosing and Preventing Burn Marks in Plastic Injection Molding
Dark specks, streaks, and degraded areas on the surface of molded plastic fabrication point to a common molded defect: burn marks. The discoloration and damage arises when trapped gases in the mold combust or degrade the hot resin. Preventing burn marks requires addressing root causes like inadequate venting, poor mold cooling, excess material moisture, and incompatible process settings. This guide covers burn mark causes, identification, and proven methods for eliminating them.
What Are Burn Marks?
Burn marks, also called dieseling, are unsightly blemishes, specks, streaks, and patches on the surface of molded plastic parts. The darkened, degraded areas form when high mold surface temperatures and residual trapped gases interact destructively with the hot molten resin.
Though just cosmetic rather than structurally compromising, burn marks detract from part appearance and quality. The unsightly defects typically result from processing issues rather than material problems.
Identifying Burn Marks
Common characteristics of burn marks include:
- Dark specks or streaks on the surface
- Degraded, matte patches with loss of gloss
- Black, brown, or rust colored discoloration
- Pitted, rough surface texture in affected areas
- Often concentrated in particular mold regions
- Usually inconsistent, unpredictable location
Inspecting parts across multiple cavities reveals whether burn marks concentrate in specific areas. This points to localized molding issues.
What Causes Burn Marks?
Burning arises from trapped gases degrading the hot plastic:
- Inadequate venting – Air pockets in the mold combust gasses when compressed. Added vents are needed.
- Insufficient cooling – Excessive mold surface temperature decomposition gases. Better cooling is required.
- Moisture contamination – Water vapor from improper resin drying degrades material.
- Overheated nozzle – Partial burning of plastic from excessive nozzle temperature.
- Degraded material – Contaminants and improper processing can release combustible gases.
Addressing the root issue is key, as burning is merely a symptom.
Preventing Burn Marks Through Proper Venting
Ensuring adequate mold venting is the foremost way to prevent burning. Properly incorporating vents provides outlets for gases to safely evacuate from the cavity during filling and packing.
Venting considerations for preventing the marks:
- Add vents in hot spot areas showing burns. Double vents may be needed.
- Adjust vent land length; shorten for thin parts. Land must remain unclogged.
- Ensure vent channels offer unobstructed exhaust paths from cavity to atmosphere.
- Increase overall venting area. Use maximum allowable shutoff clearance.
- Verify vents are not occluded by clamp pressure. Adjust if angled.
Robust venting designed specifically for the part geometry resolves most burning issues.
Improving Cooling to Avoid Burn Marks
For molds already adequately vented, ensuring sufficient mold cooling prevents excessive temperatures that degrade trapped gases into burning byproducts.
Cooling methods to prevent burning include:
- Remediating hot spots with added cooling lines or channels. Double up lines if needed.
- Maximizing water flow rate through cooling circuits.
- Lowering water temperature incrementally for greater heat transfer.
- Installing bubblers or other agitation to improve water convection.
- Reducing cycle times to limit heat soaking.
Additional strategic cooling maintains safe mold surface temperatures.
How Improper Drying Causes Burning
Even tiny amounts of moisture from inadequate resin drying can cause burning. Water vapor creates volatile gases when subjected to high molding temperatures and pressures.
Follow material supplier recommended pre-drying times and temperatures. Other tips:
- Verify resin dryness level using moisture analysis.
- Prevent reabsorption of moisture after drying with sealed containers.
- Dry parts between multiple process steps.
- Ensure dryers are functioning properly and desiccant is fresh.
Excluding all moisture from the resin prevents its gasses from burning in the mold.
Preventing Burn Marks Through Process Settings
Adjusting process parameters can also help avoid burning:
- Lower melt and mold temperatures incrementally if able.
- Increase injection speeds for faster cavity filling.
- Reduce or eliminate short shots that increase trapped gases.
- Optimize packing profile – higher pressure or time as able.
- Check and recalibrate process monitoring if controls are drifting.
Tweaked temperatures, speeds, pressure, and duration balance fill and protect against burns.
Tooling Factors to Eliminate Burning
Tooling and mold factors also impact burning defects:
- Polished vents prevent material adherence obstructing venting.
- Abrasion-resistant, non-corrosive mold materials avoid roughened tooling.
- Manganese copper alloys like G200 resists heat checking.
- Address worn, damaged, or galled tooling.
- Replace corroded, oxidized nozzle tips if burning near gate.
Plastic Manufacturer are properly specifying and maintaining tooling also avoids conditions favoring burn defects.
Conclusion
While burn marks damage aesthetic appeal more than function, these unsightly defects still indicate suboptimal molding conditions. Comprehensive strategies like adding properly designed vents, strategically improving cooling, drying materials thoroughly, optimizing process settings, and maintaining high-quality tooling are effective ways to banish it from molded plastic parts. A systematic, well-instrumented approach identifies the true underlying factors enabling permanent prevention. This avoids iterative guesswork and speeds time to market with robust production of flawless components.
In summary, preventing the marks in plastic molding requires:
- Adequate venting designed based on part geometry
- Targeted cooling improvements to remediate hot spots
- Stringent resin drying protocols before molding
- Optimized process settings for fill, pack, temperature
- Properly specified and maintained tooling
With the right synergistic solutions implemented, manufacturers can eliminate the costly headaches of burn marks marring plastic molded components.